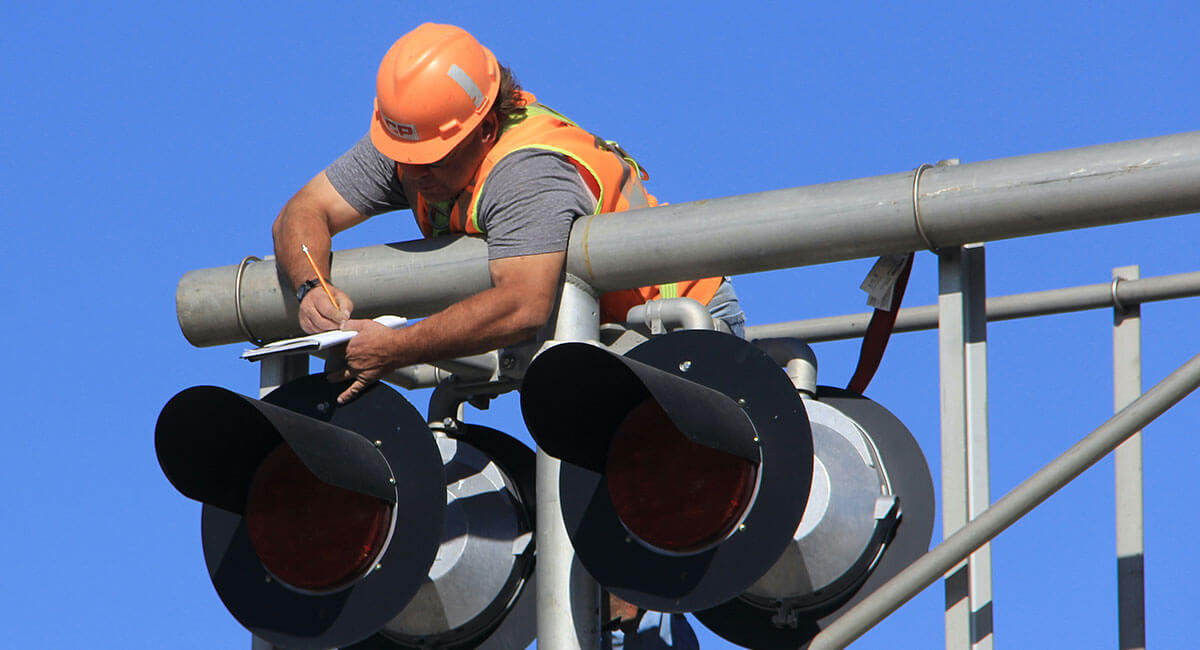
In this blog I will share my experience of using AWS IoT (Internet of Things) for predictive maintenance across different machines in IIoT (Industrial Internet of Things).
Predictive maintenance
Predictive maintenance is about prediction of your maintenance requirements in a well informed manner using real time data collected from sensors attached to the components. Your machine can have many components and some specific component may require maintenance not the whole machine. Taking the example of a car, if it's about engine maintenance we know that by only performing regular oil changes will work to save us costly maintenance (Based on prediction on kilometers travelled).
The same is the case with industrial mechanical machines, you can apply predictive models on machine data (collected through sensors) to predict about the life/wear and tear of particular components in advance. This can save you on extra and unplanned maintenance of the whole machinery. For example if a particular motor is heating up or vibrating excessively this would indicate pending failure. In that case only that particular motor needs overhaul, so you will save on overall inspection of the machinery on a time to time basis.
Use case for Carousel
A luggage carousel is composed of different motors, wheels and carbon components.
These components can be affected by overweight or misplaced luggage.
The above usage causes the motors to undergo abnormal friction and therefore temperature rise.
Overweight and misplaced luggage on the carousel can result in flexing and cause the motor ‘s sliding motion to perform abnormally and ultimately can cause halt of the whole carousel.
When the carousel is in halt or malfunctioning state then it can cause delays to flights due to passengers and connecting flights waiting for luggage and passengers can even lose baggage on arrival to their destinations. So these delays can ultimately result in loss of millions of dollars to airport flight operations.
One carousel can have different components/machines which work in conjunction to achieve transport over the belt. These include motors, slats, speed generators. In order to get data from these components we have used different sensors that send their data to AWS IoT Cloud as below
Carousel Id:
NorthLine15
Illuminance Range:
0 [No light, Healthy Slat], 1 [Light found, Broken Slat]
Tensile Strength:
Acceptable [5–10] non acceptable [>10 or <5]
Tachometer Speed:
12 RPM
Vibration:
Low [<5] Normal[5–10] High [>10]
For this project, I have used sensors from IFM and Cloud gateway from CloudRail.
With a combination of AWS IoT Services and the above hardware providers, I have designed and implemented my architecture as below.
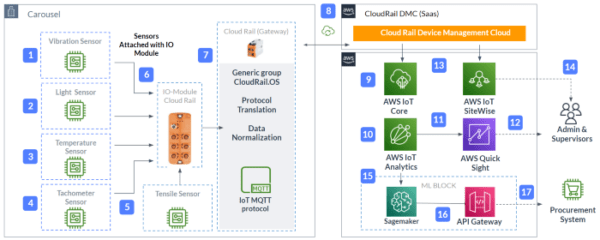
This architecture explains following steps
1–5
Installation of Vibration, Light, Temperature, Tachometer and Tensile Sensors
6–7
Connection of sensors with I/O link module and Cloud Gateway
8
CloudRail Device Management Cloud for definition of sensors and its connection to AWS IoT
9-10
Unstructured IoT Data flow from CloudRail DMC to AWS IoT Core and through AWS IoT Core ‘s rule based engine shifted to AWS IoT Analytics for Data processing through pipe line where unstructured data from IoT sensors is filtered, transformed and enriched.
11-12
The enriched data is utilized in SPICE Datasets of AWS Quick Sight for graphical output. The graphical output is used by factory users for different insights.
13-14
The raw data is utilized in AWS IoT SiteWise for display. AWS IoT SiteWise already has asset modelling defined for sensors and Cloudrail can easily integrate directly with AWS IoT SiteWise. End users can see this data directly through the AWS SiteWise monitor dashboard.
15–17
Enriched data is utilized by trained dataset in AWS Sagemaker (trained using Linear Regression Algorithm on machine sensor data) and based on Machine learning model evaluation we can invoke AWS API gateway which can procure specific machine maintenance parts and services.
I am able to output the following insights using AWS QuickSight.
Vibration variations when the carousel is overloaded or in idle mode e.g. In this graph we can see that the NorthLine15 carousel is having more vibrations on sampled 1st rounds.
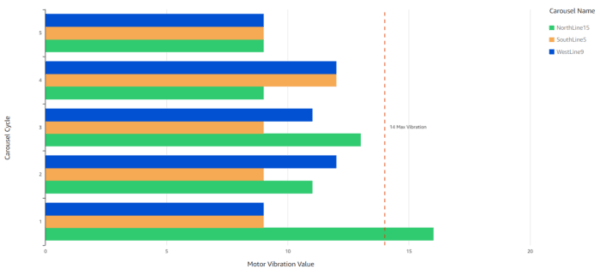
Motor temperature variance in crowded carousel operations. e.g. in this graph we can see SouthLine5 is getting increased temperatures in a couple of rounds.
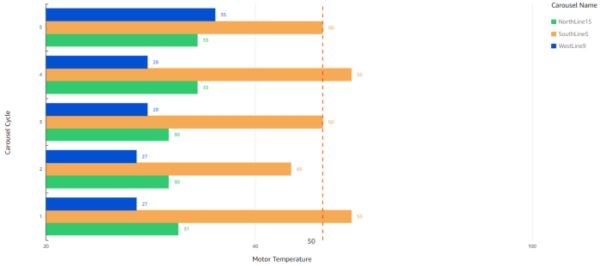
Slat fault detection with Light Sensors. Here we are detecting slat difference on straight and curved paths and here we can see Northline15 is having slat bending or misplacement or tearing detected in a couple of rounds.
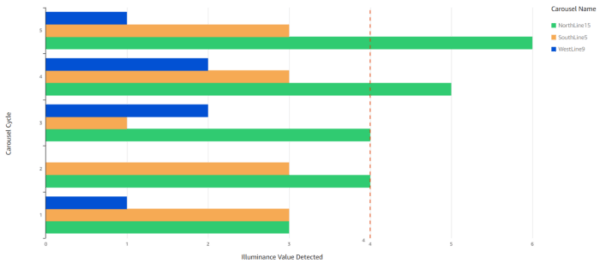
After the initiation of an automatic order by machine learning algorithm in the procurement system, the following notification is sent to the procurement manager for approval.
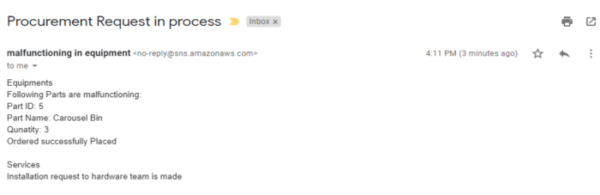
AWS Services
Following AWS services are used:
AWS SageMaker | AWS APIGateway | AWS IoT Analytics |
AWS QuickSight | AWS SNS | Cloudrail Device management Cloud
Pricing
AWS IOT Services cost for Ireland region based for 90 sensors with predictive analysis is around 430 USD. Detailed breakup cost is as here https://bit.ly/3r23MLw
You will require particular sensors e.g. Motor speed, Vibration, Temperature and Tachometer sensors which you can get using IFM and for IOT gateway you can refer to Cloud rail.
For try on services for AWS IOT are available with zero cost in free tier mode for 12 months. You can send 250 K Messages (published or delivered) per month.